Aerospace Chrome Plating In Florida
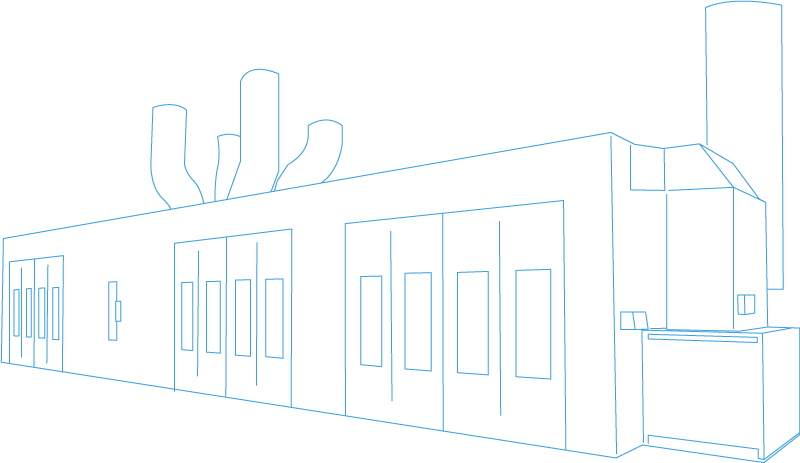
Employees
Square Footage
Processes
Processes
Parts Per Year
Processing Capabilities
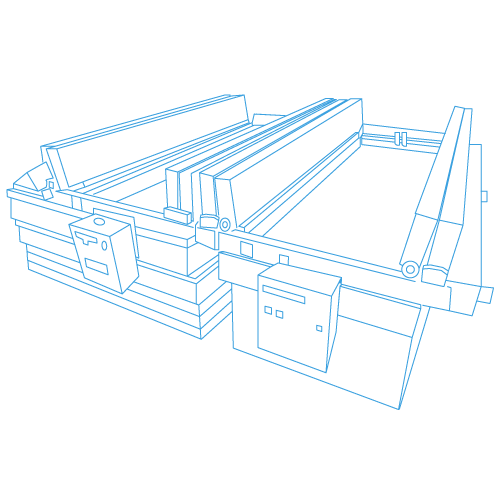
NDT
Hardness/Conductivity
Magnetic Particle
Penetrant
Painting / Coatings
Dry Lube
Fuel Tank Coating
Primer
Topcoat
Sol Gel
Additional Services
Part Mark
Shot Peen
Chemical Processing Aluminum
Anodize Phosphoric (PAA)
Anodize – Type I Chromic
Anodize – Type II Sulfuric
Chemical Film – Type 1 (Chromicoat L25)
Chemical Film – Type 1 (Alodine 1132)
Chemical Film – Type 2 (Chemeon TCPHF)
Chemical Processing Hard Metals
Passivation Type VI
Titanium Etch (Pickle)
Customer Portal
Valence News
Corrosion Vs Oxidation: Key Differences In Metal Degradation And Protection Techniques
Corrosion vs oxidation—learn the key differences, effects on metals, and best protection techniques. Get expert insights from Valence today!
Tinned Copper Vs Bare Copper: Which Is Better For Electrical Applications?
Tinned copper vs bare copper—Valence breaks down the pros, cons, and best uses for each. Learn which is right for your electrical applications today!
Is Anodized Aluminum Safe? Exploring Its Uses And Benefits In High-Performance Industries
Is anodized aluminum safe? Learn about its uses and benefits in high-performance industries. Understand its safety and applications.
Does Nickel Rust? Understanding Nickel’s Resistance To Corrosion In Aerospace Applications
Does nickel rust? Learn how nickel resists corrosion in aerospace applications. Valence breaks it down—read now for key insights!
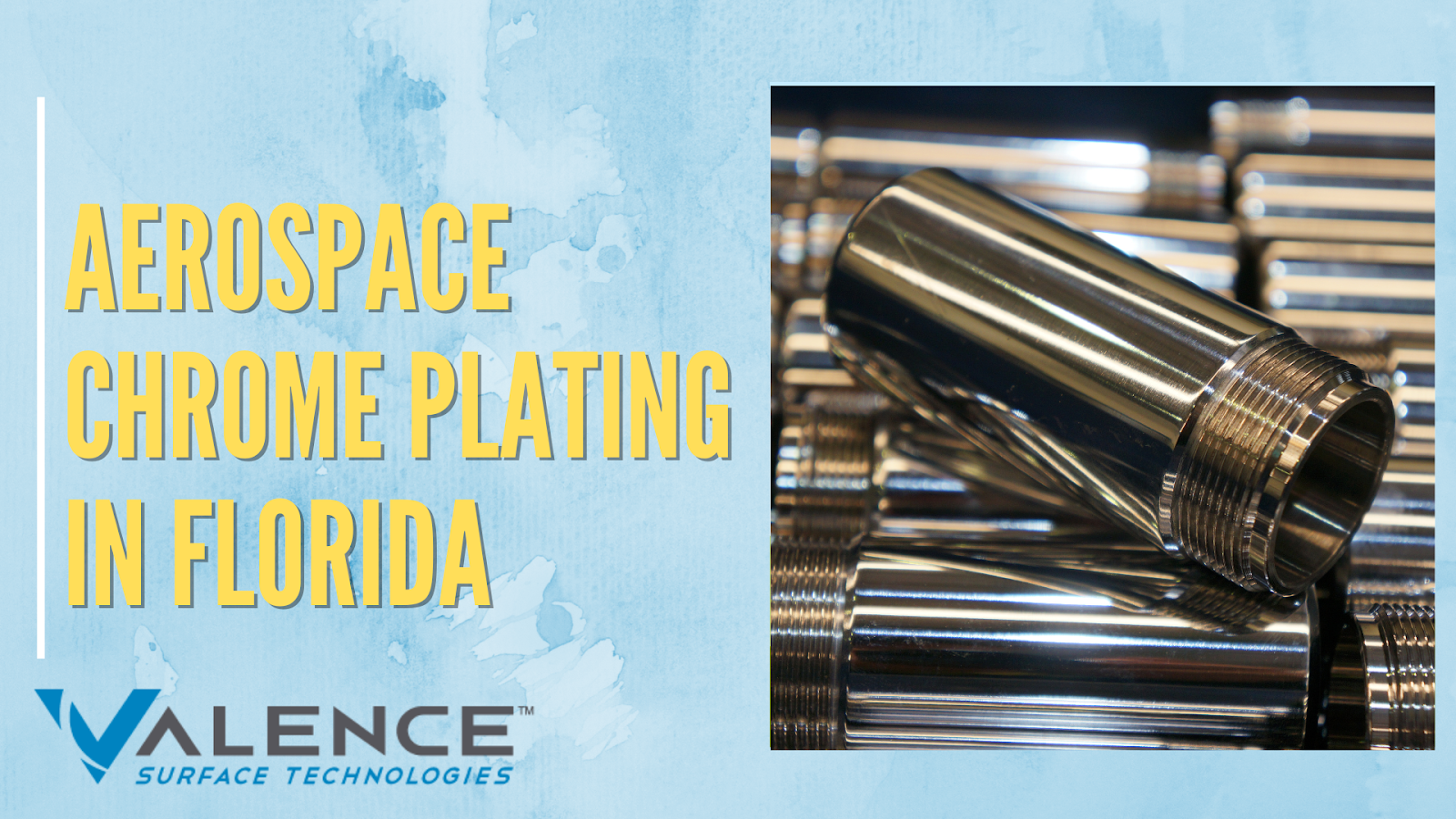
What Is Aerospace Chrome Plating?
Aerospace chrome plating is a specialized electroplating process where a thin layer of chromium is deposited onto aerospace components to enhance their performance and durability. This technique is widely used to improve wear resistance, reduce friction, and protect against corrosion and environmental factors. Chrome plating is particularly valued for its hardness and ability to withstand extreme operating conditions, such as high temperatures and mechanical stress, making it ideal for critical aerospace applications.
In aerospace, chrome plating is commonly applied to components like landing gear, hydraulic systems, engine parts, and structural elements. It ensures that these parts maintain integrity and functionality under demanding conditions, including high-altitude pressure changes and exposure to corrosive elements.
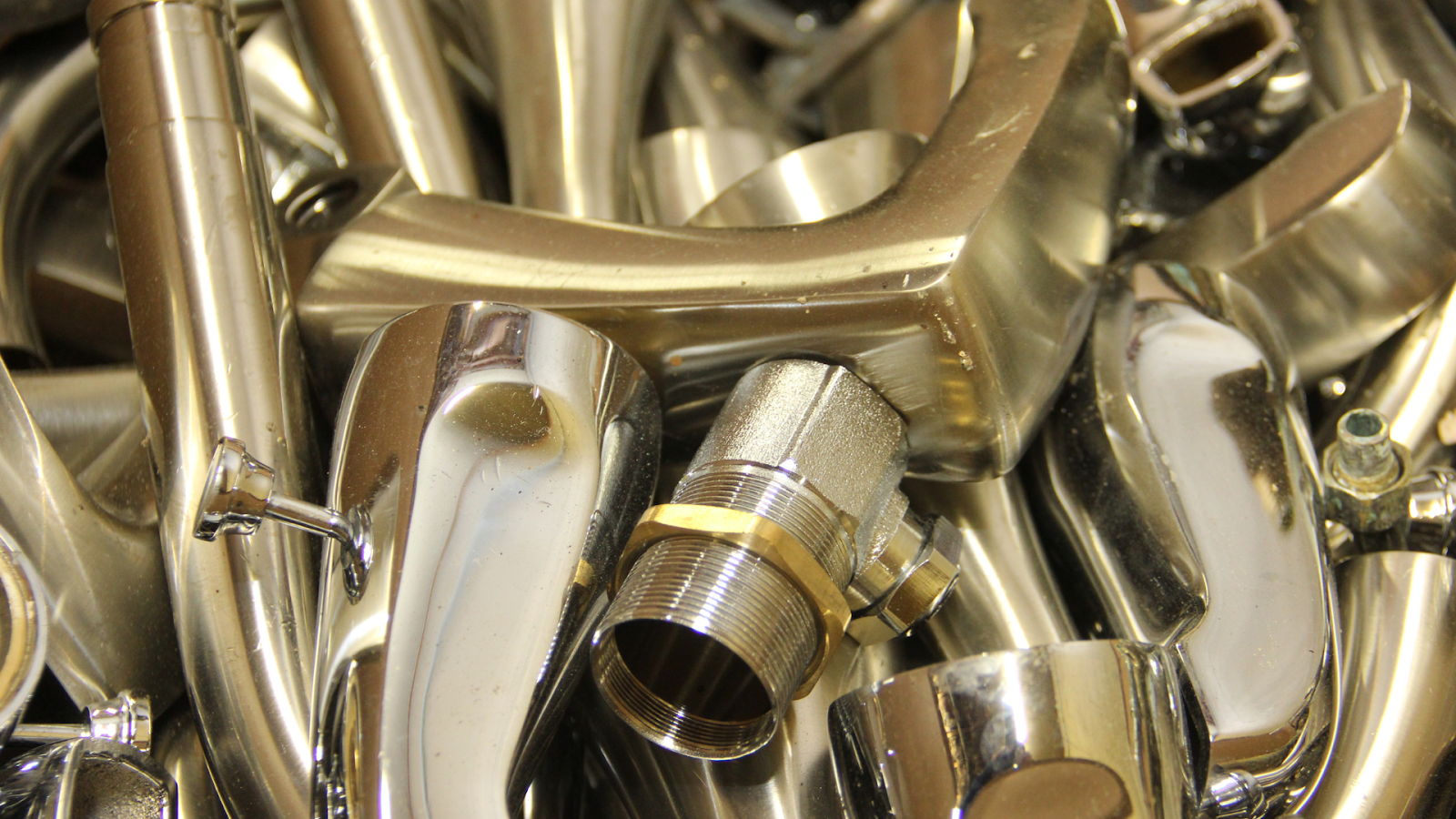
Elevate Your Aerospace Projects With Valence Surface TechnologiesUnlock a world of possibilities with Valence, the global leader in aerospace surface finishing. Here’s why Valence is your ultimate partner:
Join the industry leaders who choose Valence Surface Technologies for their aerospace finishing needs. Request a customized quote for your finishing solutions today. |
Why Choose Valence Surface Technologies For Aerospace Chrome Plating?
Here’s why Valence should be your go-to provider for aerospace chrome plating:
Unmatched Expertise In Aerospace
Valence has cemented its position as the world’s largest independent aerospace product finishing company. This distinction is not just about scale; it reflects our deep-seated expertise and comprehensive understanding of the aerospace industry’s needs. Our team of experts possesses the technical knowledge and experience required to handle the sophisticated chrome plating demands of aerospace components. This ensures that every project meets the sector’s stringent quality and compliance standards.
Complete Integrated Solution
Unlike other service providers, Valence offers a truly integrated solution for aerospace surface finishing. Our operations are not limited to chrome plating; we provide a full spectrum of surface treatments, allowing our clients to benefit from a cohesive and streamlined finishing process. This integration reduces logistical complexities, ensures consistency in quality, and can significantly shorten project timelines. For aerospace companies in Florida and beyond, Valence is the only provider that offers such a comprehensive approach to surface finishing.
Proven Track Record
Valence Surface Technologies boasts a proven track record of success in delivering top-tier aerospace chrome plating services. Our portfolio includes partnerships with renowned companies, demonstrating our capability to meet the demanding and varied surface finishing needs of the aerospace industry. This legacy of excellence positions Valence as the preferred choice for companies seeking the best chrome plating in Florida.
Aerospace Chrome Plating Process
Below is a step-by-step breakdown of the aerospace chrome plating process.
Inspection And Pre-Treatment
Before the plating process begins, the components undergo a thorough inspection and pre-treatment to ensure the surface is prepared for chrome application. This phase is crucial for achieving a uniform and high-quality finish.
Key Steps:
- Inspection:Technicians check the components for surface defects, contamination, and structural integrity.
- Masking:Areas of the component that should not be plated are masked using specialized materials to protect them during the plating process.
- Surface Preparation:The surface is prepared by degreasing and cleaning to remove oils, dirt, and residues. Common cleaning methods include ultrasonic cleaning, vapor degreasing, or alkaline baths.
Surface Activation
Surface activation ensures the metal can bond effectively with the chromium layer. This step enhances the adhesion between the base metal and the chrome plating.
Key Steps:
- Acid Etching:The component is immersed in an acid solution to remove oxidation layers and activate the surface.
- Mechanical Preparation: In some cases, surfaces are mechanically treated, such as grit blasting or grinding, to ensure the part is smooth and free of imperfections.
Electroplating Process
The electroplating stage is the core of the chrome plating process. It involves applying chromium to the surface of the metal component using an electrolytic solution.
Key Steps:
- Setup:The prepared component is suspended in a chrome plating bath containing a chromium solution (typically hexavalent or trivalent chromium compounds).
- Electrical Current:An electrical current is passed through the solution. The component acts as the cathode (negative electrode), while the chromium anodes dissolve into the electrolyte solution.
- Deposition: Chromium ions are deposited onto the component’s surface, forming a thin, uniform chrome layer. The thickness of the chrome layer is carefully controlled to meet specific requirements.
- Bath Monitoring: Throughout the process, temperature, current density, and solution composition are monitored to ensure consistency and quality.
Post-Treatment And Finishing
After the chrome plating process, the component undergoes post-treatment steps to refine the finish, ensure durability, and meet quality standards.
Key Steps:
- Rinse And Neutralization: The plated component is rinsed thoroughly to remove residual chemicals and neutralized to prevent surface reactions.
- Polishing And Buffing:The plated surface is polished to achieve the desired smoothness and reflectivity. This step is particularly important for aesthetic or functional requirements like friction reduction.
- Deburring:Any imperfections or rough edges are smoothed out to ensure the part meets dimensional and performance specifications.
Inspection And Quality Assurance
Once the component is plated and finished, it undergoes a final inspection and series of tests to confirm it meets the aerospace industry’s stringent standards.
Key Tests:
- Thickness Testing:Ensures the chrome layer is of uniform and appropriate thickness for the application.
- Adhesion Testing: Confirms the chrome layer is firmly bonded to the base material.
- Hardness Testing:Verifies the increased hardness achieved through chrome plating.
- Corrosion Resistance Testing: Evaluates the component’s ability to resist rust and degradation in harsh environments.
- Dimensional Inspection:Confirms that the plating process has not affected the component’s critical dimensions or tolerances.
Benefits Of Aerospace Chrome Plating
Here’s how our chrome plating services benefit our clients:
Enhanced Durability And Wear Resistance
Chrome plating significantly increases the surface hardness of aerospace components, making them more resistant to wear and tear. This is critical in prolonging the lifespan of parts subject to high friction levels and needing to maintain their dimensional integrity over time.
Improved Corrosion Resistance
Aircraft and space vehicles operate in some of the most challenging environmental conditions – from the corrosive, salty air of sea-level operations to the vacuum of space. Chrome plating adds a protective layer that shields components from oxidation and corrosion, ensuring they perform optimally.
Reduced Friction
The smooth surface finish achieved through chrome plating reduces friction between moving parts. This is invaluable in aerospace applications where efficiency and precision are paramount. Lower friction means less energy waste, leading to more efficient operation and reduced fuel consumption.
Aesthetic Appeal
Beyond functional benefits, chrome plating provides aerospace components a sleek, polished look. This aesthetic appeal is important for parts visible to the end-user, contributing to a perception of quality and attention to detail.
Cost-Effectiveness
Investing in chrome plating can lead to long-term cost savings for aerospace companies. By extending the service life of components, reducing the need for frequent replacements, and minimizing downtime due to maintenance, chrome plating proves to be a cost-effective solution for surface finishing.
Aerospace Chrome Plating Applications
Aerospace chrome plating is vital for improving various aircraft components’ durability, safety, and performance. Its applications span multiple systems, offering wear resistance, corrosion protection, and enhanced functionality. Here’s a concise look at its key uses:
Landing Gear Components
- Purpose: Withstand heavy loads during takeoff and landing.
- Benefits: Abrasion resistance, corrosion protection, and smooth surface finishes for precise operation.
- Examples: Landing struts, axles, and hydraulic actuators.
Hydraulic Systems
- Purpose: Ensure reliable performance in flight controls and brakes.
- Benefits: Reduced friction, leak prevention, and durability under high pressure.
- Examples: Piston rods, cylinders, and sealing surfaces.
Engine Components
- Purpose: Enhance engine performance under extreme conditions.
- Benefits: Heat resistance, wear protection, and oxidation prevention.
- Examples: Compressor blades, turbine shafts, and valve seats.
Actuation Systems
- Purpose: Control movements of wings, rudders, and stabilizers.
- Benefits: Dimensional stability, low friction, and corrosion protection.
- Examples: Actuator rods and servo mechanisms.
Structural Components
- Purpose: Reinforce airframe and fuselage supports.
- Benefits: Load resistance, environmental protection, and a polished finish.
- Examples: Wing struts and fasteners.
Rotational Parts
- Purpose: Improve longevity and efficiency of moving components.
- Benefits: Reduced wear, extended lifespan, and improved balance.
- Examples: Shafts, bearings, and rotors.
Fuel and Fluid Systems
- Purpose: Maintain integrity and flow in fuel lines and fluid systems.
- Benefits: Corrosion resistance, sealing efficiency, and durability under pressure.
- Examples: Valves, fittings, and injectors.
Pricing Information For Aerospace Chrome Plating
At Valence, we understand that every component plays a critical role in the performance and safety of aerospace equipment. That’s why we employ a comprehensive quoting process that considers:
- Material and Preparation Requirements: Different materials may require specific pre-treatment processes to ensure optimal adhesion and performance of the chrome plating.
- Surface Area and Complexity of the Component: Larger or more complex parts necessitate more labor and materials, impacting the overall cost.
- Quality and Compliance Standards: Adherence to stringent aerospace quality standards, such as AS9100, can influence the pricing due to the meticulous inspection and testing required.
- Volume and Frequency of Orders: We offer scalable solutions and competitive pricing for small-scale prototypes and large production runs, with special pricing considerations for long-term contracts.
For a precise quotation, we encourage interested companies to contact us directly with their project specifications. Our team of experts is ready to review your requirements and provide a detailed breakdown of the costs involved.
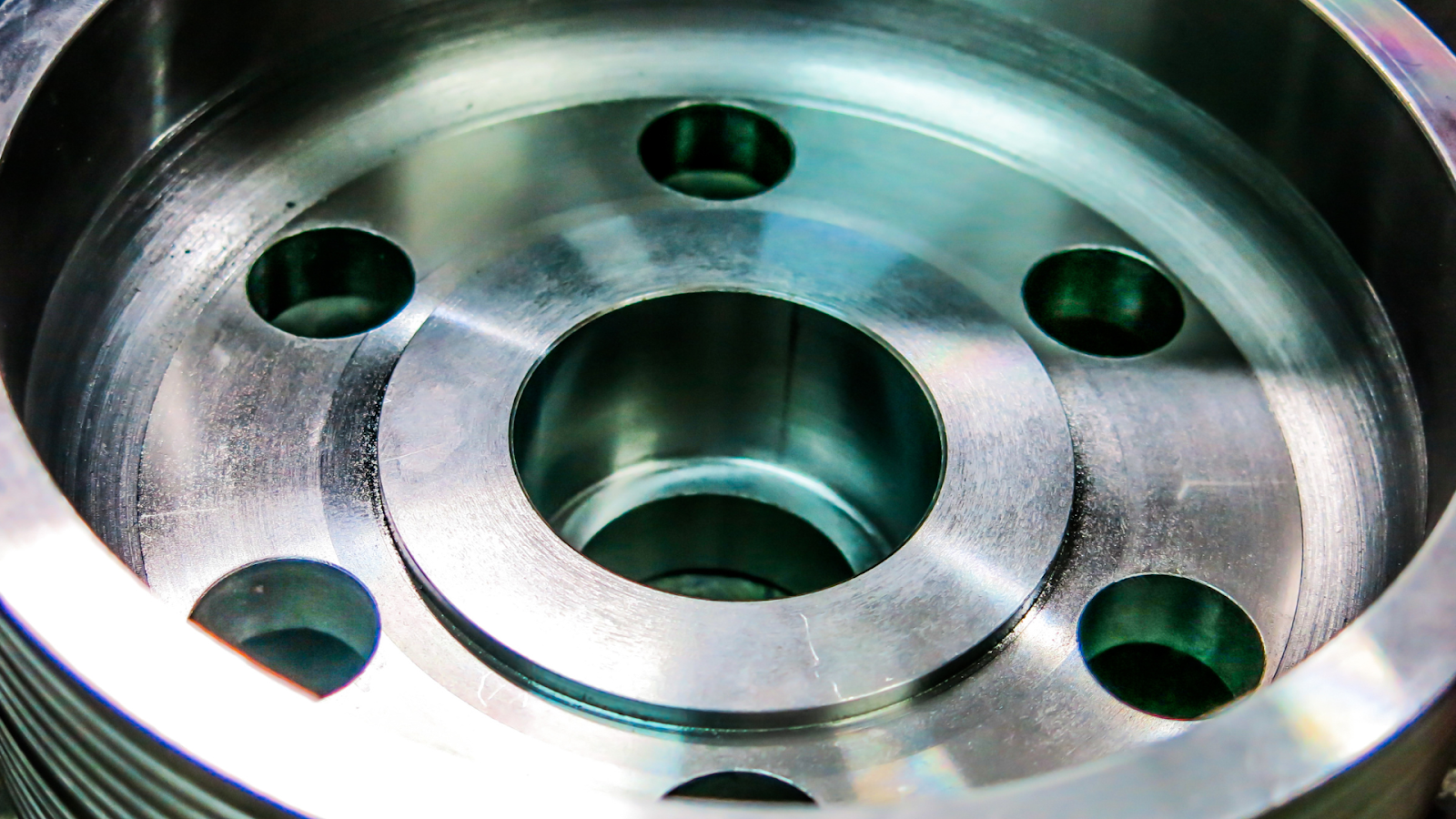
Exploring Valence Surface Technologies’ Eastern Locations
Valence Surface Technologies proudly extends its aerospace surface finishing services across the Eastern United States. With facilities strategically located in key aerospace hubs, we cater to the specific needs of the aerospace, aviation, and defense industries, ensuring precision, quality, and environmental responsibility at every production stage.
Valence Surface Technologies – Atlanta, GA
Located in the heart of Atlanta, Georgia, one of the nation’s major aerospace hubs, this facility plays a critical role in our network. Atlanta’s strategic positioning in the Southeast makes it an ideal location for providing a wide range of aerospace surface finishing services, meeting the diverse needs of the aerospace and aviation industries.
Services Offered:
- Anodizing: Our anodizing services enhance the corrosion resistance and surface hardness of components, particularly for aluminum parts used in aerospace applications.
- Passivation: We improve the resistance of stainless steel and other metals to corrosion, ideal for aerospace components exposed to challenging environments.
- Chemical Conversion Coatings: This service provides an additional layer of corrosion protection for aluminum and other metals, ensuring the longevity and reliability of critical aerospace parts.
Valence Surface Technologies – Greenville, SC
Situated in Greenville, South Carolina, our facility specializes in aerospace coatings and finishes. Greenville is known for its robust aerospace industry presence, making this location a hub of innovation and support for aerospace manufacturers, suppliers, and MRO (maintenance, repair, and overhaul) providers in the region.
Services Offered:
- Aerospace Coatings: We provide specialized coatings designed to protect components from wear, corrosion, and extreme temperatures, ensuring long-term reliability.
- Aerospace Surface Finishing: A comprehensive range of surface treatments designed to enhance the durability, performance, and aesthetic appearance of aerospace components.
Valence Surface Technologies – Orlando, FL
Our Orlando, Florida, facility plays a key role in serving the aerospace and defense sectors with a wide range of surface finishing solutions. Orlando’s proximity to major aerospace and defense contractors positions this location perfectly to meet the stringent demands of these industries.
Services Offered:
- Surface Finishing Solutions: We offer a range of plating, coating, and finishing services that enhance the performance and longevity of aerospace components.
- Specialized Aerospace Coatings: Our Orlando location provides coatings that enhance resistance to extreme temperatures, wear, and corrosion, ensuring optimal performance under challenging conditions.
Valence Surface Technologies – Raleigh, NC
Located in Raleigh, North Carolina, our facility is dedicated to providing cutting-edge aerospace surface treatments. Known for its sustainability initiatives and strict adherence to industry standards, the Raleigh facility stands at the forefront of aerospace finishing innovation.
Services Offered:
- Sustainable Surface Treatments: Raleigh leads our efforts in environmentally responsible aerospace finishing by offering water-based coatings and eco-friendly passivation processes.
- Adherence to Industry Regulations: With certifications like NADCAP and AS9100, our Raleigh location ensures that all aerospace components meet the highest quality and safety standards.
Contact Valence Surface Technologies Today
Valence Surface Technologies is your premier partner for companies in the aerospace, defense, and space industries seeking unparalleled chrome plating services in Florida. Our commitment to excellence is reflected in our status as the world’s largest independent aerospace product finishing company. At Valence, we understand the critical importance of precision and reliability in aerospace surface finishing. We offer a unique, fully integrated solution, ensuring a seamless experience from start to finish.
Our state-of-the-art facilities in Florida are equipped with advanced chrome plating technology, catering to the specific requirements of the aerospace sector. The expertise of our highly trained technicians, combined with our commitment to quality, ensures that your components meet the stringent standards required for aerospace applications.
For inquiries and to schedule a consultation, visit our website atValence Surface Technologies or reach out directly through our contact page. Your pursuit of excellence in aerospace surface finishing starts with Valence.
Frequently Asked Questions About Aerospace Chrome Plating In Florida
What certifications are required for aerospace chrome plating companies in Florida?
To ensure the highest quality and safety standards in aerospace chrome plating, companies in Florida are required to have several certifications, including but not limited to Nadcap (National Aerospace and Defense Contractors Accreditation Program), AS9100 (Quality Management System standard for the aviation, space, and defense industries), and ISO 9001 (Quality Management). These certifications attest to a company’s ability to meet stringent aerospace industry standards and regulatory requirements.
What materials can be chrome plated for aerospace use?
In the aerospace industry, a variety of metals and alloys can undergo chrome plating, including aluminum, steel, stainless steel, copper, and brass. These materials are commonly used in components such as landing gear, turbine engines, and hydraulic systems, where enhanced surface properties such as corrosion resistance, increased hardness, and reduced friction are critical.
Is aerospace chrome plating in Florida environmentally regulated?
Yes, aerospace chrome plating in Florida is subject to rigorous environmental regulations to minimize harmful emissions and ensure the protection of the environment. The process involves the use of hazardous chemicals, and as such, companies must adhere to specific state and federal guidelines, including those mandated by the Environmental Protection Agency (EPA) and the Occupational Safety and Health Administration (OSHA), to mitigate environmental impact and ensure worker safety.
How long does the chrome plating process take?
The duration of the chrome plating process can vary significantly depending on several factors, such as the size and complexity of the parts being plated, the specific type of chrome plating (e.g., hard chrome or decorative chrome), and the desired thickness of the plating layer. Generally, the process can take anywhere from a few hours to several days.
Can chrome plating repair worn aerospace parts?
Yes, one of the significant advantages of chrome plating is its ability to restore worn or damaged aerospace parts to their original dimensions or to improve their wear resistance. By depositing a layer of chrome onto the surface of the component, the process can fill in scratches, corrosion damage, and other forms of wear, extending the part’s service life and reducing the need for costly replacements.
What quality control measures are in place for aerospace chrome plating?
Quality control is paramount in the aerospace industry, and as such, companies specializing in chrome plating must adhere to strict quality management practices. These include regular inspections and testing throughout the plating process, such as thickness measurements, adhesion tests, and visual inspections, to ensure that the plated components meet all specified requirements and industry standards.