Aerospace Electroless Nickel Plating In Orlando, FL
Valence Surface Technologies stands at the forefront of aerospace product finishing in Orlando, FL, particularly in handling electroless nickel plating. This highly specialized process is critical for components within the aviation, defense, and space sectors due to its remarkable attributes, such as corrosion resistance, hardness, and uniform deposit thickness over complex geometries.
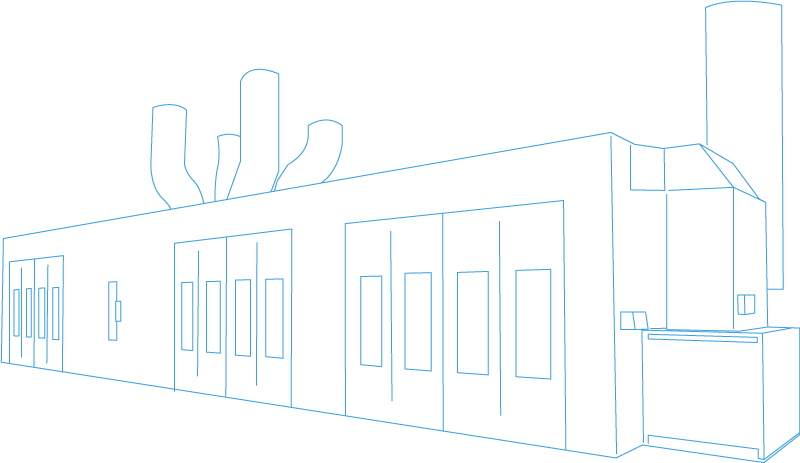
Employees
Square Footage
Processes
Processes
Parts Per Year
Processing Capabilities
NDT
Hardness/Conductivity
Magnetic Particle
Penetrant
Painting / Coatings
Dry Lube
Fuel Tank Coating
Primer
Topcoat
Sol Gel
Additional Services
Part Mark
Shot Peen
Chemical Processing Aluminum
Anodize Phosphoric (PAA)
Anodize – Type I Chromic
Anodize – Type II Sulfuric
Chemical Film – Type 1 (Chromicoat L25)
Chemical Film – Type 1 (Alodine 1132)
Chemical Film – Type 2 (Chemeon TCPHF)
Chemical Processing Hard Metals
Passivation Type VI
Titanium Etch (Pickle)
Customer Portal
Valence News
Corrosion Vs Oxidation: Key Differences In Metal Degradation And Protection Techniques
Corrosion vs oxidation—learn the key differences, effects on metals, and best protection techniques. Get expert insights from Valence today!
Tinned Copper Vs Bare Copper: Which Is Better For Electrical Applications?
Tinned copper vs bare copper—Valence breaks down the pros, cons, and best uses for each. Learn which is right for your electrical applications today!
Is Anodized Aluminum Safe? Exploring Its Uses And Benefits In High-Performance Industries
Is anodized aluminum safe? Learn about its uses and benefits in high-performance industries. Understand its safety and applications.
Does Nickel Rust? Understanding Nickel’s Resistance To Corrosion In Aerospace Applications
Does nickel rust? Learn how nickel resists corrosion in aerospace applications. Valence breaks it down—read now for key insights!
What Is Aerospace Electroless Nickel Plating?
Aerospace electroless nickel plating is a high-precision chemical process utilized to deposit a layer of nickel-phosphorus or nickel-boron alloy on the surface of a component. Unlike traditional electroplating, this method does not require an electrical current to deposit the nickel layer.
Instead, the process relies on an autocatalytic chemical reaction to uniformly coat parts of any shape or size, ensuring an even layer of nickel across complex geometries. This characteristic is particularly advantageous in the aerospace industry, where components often feature intricate designs and demand exacting standards of precision and durability.
Elevate Your Aerospace Projects With Valence Surface TechnologiesUnlock a world of possibilities with Valence, the global leader in aerospace surface finishing. Here’s why Valence is your ultimate partner:
Join the industry leaders who choose Valence Surface Technologies for their aerospace finishing needs. Request a customized quote for your finishing solutions today. |
Why Choose Valence Surface Technologies For Aerospace Electroless Nickel Plating?
Here are compelling reasons why Valence stands out in this specialized domain:
Unmatched Expertise And Capacity
Valence Surface Technologies is not just another player in aerospace surface finishing. As the world’s largest independent aerospace product finishing company, Valence brings unparalleled expertise and capacity to every project. Our comprehensive understanding of aerospace standards and requirements ensures that every component treated in our facilities meets rigorous industry specifications.
Integrated Solution Provider
Valence distinguishes itself as the only provider to offer a completely integrated surface finishing solution in an industry where the supply chain’s integrity and efficiency are paramount. This unique positioning eliminates the complexities and delays often encountered with multiple vendors, providing our clients with streamlined, efficient service that reduces turnaround times and costs.
Tailored Solutions
Recognizing that no two aerospace clients or projects are the same, Valence offers tailored electroless nickel plating solutions to meet each customer’s specific needs. Our technical team works closely with clients to understand their requirements and challenges, developing customized solutions that align with their goals and timelines.
Aerospace Electroless Nickel Plating Process
Below is a step-by-step breakdown of the process:
Surface Preparation
- Cleaning: Components are thoroughly cleaned using alkaline solutions to remove grease, oils, and contaminants.
- Mechanical Preparation: Abrasive blasting or grinding ensures the surface is smooth and free of imperfections.
Activation
- Acid Etching: The surface is etched with an acidic solution to activate it for plating.
- Catalyst Application: A catalyst, typically palladium chloride, is applied to initiate the electroless plating reaction.
Plating Process
- The component is immersed in a heated bath containing nickel salts, reducing agents (such as sodium hypophosphite), and stabilizers.
- A chemical reaction occurs, depositing a uniform nickel-phosphorus alloy layer on the surface.
- The phosphorus content can be adjusted to achieve desired properties, such as high wear resistance or increased corrosion protection.
Post-Treatment
- Rinse And Dry: The plated component is rinsed to remove residual chemicals and dried to prevent oxidation.
- Heat Treatment: The part may undergo heat treatment at controlled temperatures for added hardness and durability.
Quality Assurance
- The finished component is inspected for coating thickness, adhesion, and surface finish using advanced testing methods to meet aerospace standards.
Benefits Of Electroless Nickel Plating
Electroless nickel plating (ENP) is widely used in aerospace, automotive, and manufacturing industries due to its unique properties and advantages. Here are the key benefits:
Enhanced Wear Resistance
One of the primary benefits of electroless nickel plating is its exceptional wear resistance. The uniform coating significantly increases the lifespan of treated components by minimizing wear due to friction and abrasion. Aerospace applications often involve extreme conditions and demanding use, require components that can withstand such challenges over time. Electroless nickel plating ensures that critical components maintain their integrity longer, promoting overall system reliability.
Improved Corrosion Protection
Corrosion can severely compromise the performance and safety of aerospace components. Electroless nickel plating provides superior corrosion protection, creating a barrier that shields the base material from harsh environments and corrosive elements. This is particularly crucial in the aerospace industry, where components are frequently exposed to extreme atmospheric conditions and various corrosive substances.
Uniform Coating Thickness
Unlike traditional plating methods, electroless nickel plating achieves a consistent coating thickness over the entire component surface, including inside holes, recesses, and complex shapes. This uniformity is essential for aerospace components that demand precise dimensional tolerances and surface finishes. It ensures optimal performance and reliability, regardless of the complexity of the component’s geometry.
Conductivity And Magnetic Properties
Electroless nickel plating can be tailored to meet specific conductivity and magnetic requirements, making it an ideal choice for various aerospace applications, from electrical systems to radar and navigation. By adjusting the phosphorus content in the plating solution, Valence Surface Technologies can customize the coating to offer either increased electrical conductivity or non-magnetic properties, depending on the application’s needs.
Temperature Resistance
Aerospace components must often perform under extreme temperatures. Electroless nickel plating improves the high-temperature resistance of treated parts, ensuring they can withstand the thermal stresses encountered during operation. This attribute is vital for maintaining the component’s structural integrity and functionality in challenging aerospace environments.
Aerospace Electroless Nickel Plating Applications
Electroless nickel plating (ENP) is a critical process in the aerospace industry, offering exceptional durability, corrosion resistance, and uniformity. Here are the key applications of ENP in aerospace:
Engine Components
- Coating turbine blades, compressor parts, and engine housings.
- Provides high-temperature resistance, wear reduction, and corrosion protection.
Landing Gear Systems
- Protects struts, shock absorbers, and hydraulic cylinders.
- It enhances durability and prevents rust in harsh conditions.
Fuel And Hydraulic Systems
- Coating fuel injectors, pumps, and hydraulic actuators.
- Ensures chemical resistance and performance under pressure.
Structural And Avionics Components
- Plating fasteners, brackets, connectors, and sensors.
- Improves wear resistance, electrical conductivity, and longevity.
Space And Tooling Applications
- Protects spacecraft parts and ground support equipment.
- Provides resistance to extreme conditions and wear.
Pricing Information For Aerospace Electroless Nickel Plating
At Valence Surface Technologies, we ensure transparency in our pricing model, which is tailored to meet diverse needs. Companies seeking top-of-the-line surface finishing solutions should be aware of what factors into the pricing of these specialized services.
Factors Influencing Pricing
- Surface Complexity And Component Size: The intricate shapes and sizes of aerospace components can significantly affect the plating process’s complexity and duration, influencing the overall cost.
- Thickness Requirements: Depending on the application, the required thickness of the nickel plating layer can vary. Thicker layers necessitate longer plating times and more material, contributing to a higher cost.
- Quality And Testing Requirements: Aerospace applications often require rigorous testing and certification to ensure compliance with industry standards. These quality assurance processes add to the plating service’s cost.
Transparent Pricing Structure
At Valence Surface Technologies, we are committed to providing a transparent pricing structure that aligns with our mission to be the most trusted partner in aerospace surface finishing. Our quotes are comprehensive, including all necessary pre-treatment, plating, and post-treatment processes, ensuring no hidden fees or surprises.
Get A Custom Quote
Recognizing that every project has unique requirements, we encourage you to contact our expert team in Orlando, FL, for a customized quote. Our specialists will assess your needs, considering all the variables that impact the plating process, to provide an accurate and competitive pricing estimate.
Exploring Valence Surface Technologies’ Eastern Locations
Valence Surface Technologies proudly extends its aerospace surface finishing services across the Eastern United States. With facilities strategically located in key aerospace hubs, we cater to the specific needs of the aerospace, aviation, and defense industries, ensuring precision, quality, and environmental responsibility at every production stage.
Valence Surface Technologies – Atlanta, GA
Located in the heart of Atlanta, Georgia, one of the nation’s major aerospace hubs, this facility plays a critical role in our network. Atlanta’s strategic positioning in the Southeast makes it an ideal location for providing a wide range of aerospace surface finishing services, meeting the diverse needs of the aerospace and aviation industries.
Services Offered:
- Anodizing: Our anodizing services enhance the corrosion resistance and surface hardness of components, particularly for aluminum parts used in aerospace applications.
- Passivation: We improve the resistance of stainless steel and other metals to corrosion, ideal for aerospace components exposed to challenging environments.
- Chemical Conversion Coatings: This service provides an additional layer of corrosion protection for aluminum and other metals, ensuring the longevity and reliability of critical aerospace parts.
Valence Surface Technologies – Greenville, SC
Situated in Greenville, South Carolina, our facility specializes in aerospace coatings and finishes. Greenville is known for its robust aerospace industry presence, making this location a hub of innovation and support for aerospace manufacturers, suppliers, and MRO (maintenance, repair, and overhaul) providers in the region.
Services Offered:
- Aerospace Coatings: We provide specialized coatings designed to protect components from wear, corrosion, and extreme temperatures, ensuring long-term reliability.
- Aerospace Surface Finishing: A comprehensive range of surface treatments designed to enhance the durability, performance, and aesthetic appearance of aerospace components.
Valence Surface Technologies – Orlando, FL
Our Orlando, Florida, facility plays a key role in serving the aerospace and defense sectors with a wide range of surface finishing solutions. Orlando’s proximity to major aerospace and defense contractors positions this location perfectly to meet the stringent demands of these industries.
Services Offered:
- Surface Finishing Solutions: We offer a range of plating, coating, and finishing services that enhance the performance and longevity of aerospace components.
- Specialized Aerospace Coatings: Our Orlando location provides coatings that enhance resistance to extreme temperatures, wear, and corrosion, ensuring optimal performance under challenging conditions.
Valence Surface Technologies – Raleigh, NC
Located in Raleigh, North Carolina, our facility is dedicated to providing cutting-edge aerospace surface treatments. Known for its sustainability initiatives and strict adherence to industry standards, the Raleigh facility stands at the forefront of aerospace finishing innovation.
Services Offered:
- Sustainable Surface Treatments: Raleigh leads our efforts in environmentally responsible aerospace finishing by offering water-based coatings and eco-friendly passivation processes.
- Adherence to Industry Regulations: With certifications like NADCAP and AS9100, our Raleigh location ensures that all aerospace components meet the highest quality and safety standards.
Contact Valence Surface Technologies Today
For businesses in the aerospace, defense, and space industries seeking unparalleled surface finishing services, including electroless nickel plating in Orlando, FL, Valence Surface Technologies stands ready to meet your needs. As the preeminent leader in aerospace product finishing, Valence offers a comprehensive, integrated solution not found elsewhere in the supply chain.
We invite you to contact us today to discuss your specific surface finishing needs or to learn more about how Valence Surface Technologies can support your objectives. Our team of experts is ready to provide detailed information on our capabilities, including electroless nickel plating, and to guide you in selecting the most appropriate finishing solutions for your applications.
Frequently Asked Questions About Aerospace Electroless Nickel Plating In Orlando, FL
How does electroless nickel plating differ from traditional plating methods?
Electroless nickel plating is distinct from traditional electroplating methods due to its unique chemical process that deposits nickel onto a substrate without the use of an electrical current. This method provides a uniform coating thickness over the entire surface of the part, including on complex geometries and internal surfaces, which is often challenging to achieve with conventional electroplating techniques.
What thickness ranges can be achieved with electroless nickel plating?
Electroless nickel plating offers a wide range of coating thicknesses, typically between 0.5 and 75 microns (0.00002 to 0.003 inches). The specific thickness required for aerospace parts can be precisely controlled, enabling the exact specifications demanded by engineering requirements.
Are there any size limitations for parts that can be plated in Orlando’s facilities?
Valence Surface Technologies in Orlando, FL, has extensive capabilities for handling various sizes of aerospace components. While specific size limitations depend on the dimensions of the plating equipment, our facilities are equipped to manage both small intricate parts and large aerospace components.
What certifications should a plating service have to work with aerospace components?
A reputable plating service working with aerospace components should hold several key certifications, including AS9100D for quality management in the aerospace industry and NADCAP (National Aerospace and Defense Contractors Accreditation Program) accreditation for chemical processing. These certifications ensure the provider meets the rigorous quality standards required in aerospace manufacturing and maintenance.
How often should aerospace parts be inspected after electroless nickel plating?
The inspection frequency for aerospace parts after electroless nickel plating depends on the application and operational conditions of the parts in question. It’s crucial to adhere to the inspection protocols defined by the original equipment manufacturer (OEM) or governing regulatory bodies. For critical components, periodic inspections are necessary to monitor wear and ensure the integrity of the plating over time.
Can electroless nickel plating be applied to non-metallic aerospace materials?
Due to the chemical deposition process, electroless nickel plating is primarily used on metallic substrates. However, advancements in surface preparation techniques have made it possible to plate certain non-metallic materials, such as high-grade plastics and composites, when a conductive layer is applied to the surface. Compatibility and plating capability depend on the specific material and the desired application, requiring consultation with plating experts.