Silver Plating
Silver is a white colored, semi-precious metal, which, due to its property of high electrical conductivity, is often used in the electronics and semiconductor industries.
Due to silver’s conductivity, the microwave and satellite industries use it to carry high-frequency signals and reduce the amount of heat generated compared with copper. Another benefit is the reduction in “skin depth” generated when using silver compared to other less conductive materials.
Silver is also the best heat conductor of all metal plating materials and offers great solderability. Unlike copper, oxidized silver retains a conductive surface. Copper oxide builds resistance that is much higher than silver oxide.
Silver’s lubricity and high-temperature resistance allow engine manufacturers to use silver in the place of lubricants. It is used on bearing surfaces and anti-galling applications. Some applications might be bearings or gear teeth that are exposed to high temperatures in jet engines, or auxiliary power units where lubricants fail.
Hardness varies from about 90 Brinell to 135 Brinell hardness numbers depending on process and plating conditions. Solderability is excellent but decreases with age. Plating silver offers the best electrical conductivity, though this conductivity diminishes with time and oxidation.
Silver acts as an economically beneficial metal plating that may be put to good use for a lower price compared to other precious metals like gold or platinum.
Valence Surface Technologies has two types of silver plating available:
Matte silver plating is used in areas requiring low electrical resistance and good solderability.
Semi-bright silver plating is used where low electrical resistance isn’t a primary requirement, and in some areas where a decorative finish is desired. Semi-bright silver is more resistant to fingerprinting during assembly operations than matte silver, and it has good solderability.
Request a quote today, or contact Valence Surface Technologies for more information on any of our metal plating services.
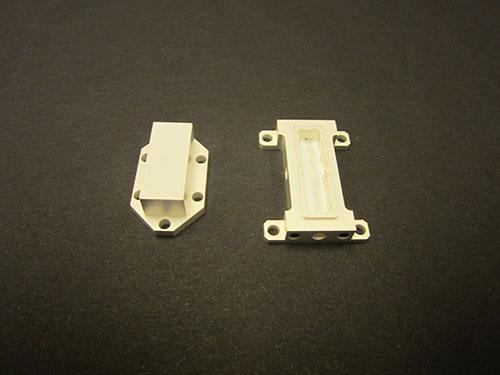
Silver Plate Process
Silver Plating
Electroplating with silver has existed for ages. It has been used since the invention of coinage and metalsmithing. Silver was first gathered in modern times as a status symbol of wealth and, more importantly, for practical industrial use. Compared to other plated metals, silver has the most uses. Silver becomes practically indispensable when used in conjunction with the majority of common industries.
In other words, it is essentially impossible to replace it with another metal. The fact that it is the least expensive precious metal is another significant point. The cost of silver plating is relatively low considering that it is currently trading at 1/60th and 1/25th of the going market prices for gold and palladium, respectively.
Further on we will discuss silver plating, its importance, benefits, and limitations. We will also talk about common silver plating issues, how to troubleshoot these issues, and why silver is an important metal in industrial plating.
What Is Silver?
Silver is a white-colored, semi-precious metal, which, due to its property of high electrical conductivity, is often used in the electronics and semiconductor industries.
Due to silver’s conductivity, the microwave and satellite industries use it to carry high-frequency signals and reduce the amount of heat generated compared with copper. Another benefit is the reduction in “skin depth” generated when using silver compared to other less conductive materials.
Silver is also the best heat conductor of all metal plating materials and offers great solderability. Unlike copper, oxidized silver retains a conductive surface. Copper oxide builds resistance that is much higher than silver oxide.
Furthermore, silver’s lubricity and high-temperature resistance allow engine manufacturers to use silver in the place of lubricants. It is used on bearing surfaces and anti-galling applications. Some applications might be bearings or gear teeth that are exposed to high temperatures in jet engines, or auxiliary power units where lubricants fail.
Hardness varies from about 90 Brinell to 135 Brinell hardness numbers depending on process and plating conditions. Solderability is excellent but decreases with age. Plating silver offers the best electrical conductivity, though this conductivity diminishes with time and oxidation.
Silver acts as an economically beneficial metal plating that may be put to good use for a lower price compared to other precious metals like gold or platinum.
What Is Electroplating?
Electroplating is the process of coating one metal or metal object with a very thin layer of another metal, typically by applying a direct electric current. This partially dissolves the metals and creates a chemical bond between them. The coating applied by electroplating is usually around 0.0002 inches thick.
The plating alters the surface of the base metal permanently by forging a chemical bond. This implies that it won’t inevitably fall off or split apart. But over weeks, months, or even years of use and wear, the plating can come off.
This top layer has very particular uses because it is so thin. Because they provide additional protection against rust, damage, and corrosion, some metals are used as coatings.
Importance Of Aerospace Plating
The majority of modern aircraft are made of titanium and titanium alloys. For aerospace crafts, titanium is highly valued because of its low density, high strength, and lightweight. Steel, aluminum, and magnesium are other regularly utilized metals.
Even though these metals are fundamental to the manufacturing of aircraft, they are not without flaws. These metals are nonetheless prone to oxidation, corrosion, and decomposition at high temperatures. Aircraft plating is utilized as a metal finishing procedure to shield aerospace metals from various risks to their integrity.
Electroplating and electroless plating are the two main plating techniques. By adopting a method called electrodeposition, electroplating entails covering a metal surface with ions of another metal.
Benefits of either type of aerospace plating include:
- Improved corrosion protection
- Enhanced strength of the metal substrate
- Increased resistance to high temperatures
- Component longevity
- Enhanced electrical conductivity
- Increased resistance to oxidation
- Aesthetic appeal
What Is Silver Plating?
Other base metals are covered with a layer of silver through the process of silver plating. Although the procedure appears straightforward, it still requires making sure that the base metal has an even layer of silver to achieve that well-known and highly desired matte-white appearance.
The end product is typically referred to as “electroplated nickel silver” when the process is carried out over nickel silver.
The procedure is frequently applied to materials like copper, steel, titanium, graphite, ceramic, plastic, and aluminum, in addition to nickel and silver.
What’s The Silver Plating Process
The silver plating process includes:
Inspection
Prior to electroplating, you should always inspect the component for flaws, such as cold joints or jagged edges, and make any necessary corrections. Otherwise, the substrate’s quality will decline, which might be problematic for your clients.
Pre-Treatment
Before plating your metal part, finish any pre-treatments that are required. Additionally, you ought to underplate with nickel, copper, or both metals. If you want to achieve a particular result, you can also add a silver strike or an anti-tarnish coating. The silver layer should be 0.0005 inches thick, for a total of 0.0010 inches, if the nickel or copper layer is 0.0005 inches thick.
Electroplating
With electroplating, the substrate is immersed in a solution of silver ions. The ions deposit onto the part’s surface, coating it in your chosen metal—in this case, silver—after running an electric current through the solution.
Silver Plating Methods
Some methods for silver plating are:
Barrel Plating
If you need to simultaneously plate a large number of small parts, try barrel plating. The substrates are placed inside a non-conductive, barrel-shaped cage. In an electrolytic solution of silver ions, this cage is immersed, and each of the pieces makes a bipolar connection to the other. As a result, plating efficiency is increased and is more uniform.
Rack Plating
Rack plating involves fastening a substrate to a rack with screws or hooks, which then immerses the metal component in an ionic solution. The silver ions are applied to the product by an electric current that is conducted by the screws. If you’re working with larger, more delicate pieces, use this approach.
Types Of Silver Plating
Bright Silver Plating
Silver is the metal with the highest electrical conductivity, but it does not qualify as a noble metal. Because it readily tarnishes and forms silver nitrate or silver sulfide on the surface when exposed to chlorides or sulfides, bright silver is frequently classified as a semi-precious metal. The best applications for bright silver plating include those requiring high electrical and/or thermal conductivity, lubricity and/or wear resistance in bearing applications, solderability in lighting and/or LED applications, and optical reflectivity.
Silver is currently one of our most popular connector finishes, especially for connector applications in automobiles. To increase shelf life and stall the tarnish of bright silver, surface treatments can be added.
At Valence Surface Technologies, we use semi-bright silver plating. Semi-bright silver plating is used where low electrical resistance isn’t a primary requirement, and in some areas where a decorative finish is desired. Semi-bright silver is more resistant to fingerprinting during assembly operations than matte silver, and it has good solderability.
Matte Silver Plating
Primarily used as a wire-bondable surface in lead frames, integrated circuits, or sensor applications, matte silver is another option for many of our clients. Because a matte silver deposit does not include the metallic hardening agents that are present in bright silver, it is softer than bright silver and not generally appropriate for separable connector applications where wear is an important consideration.
Benefits Of Plating Silver
Silver electroplating has several special advantages because of the practical, high-quality nature of this metal. There are many great reasons to employ this technique when creating your next batch of metal components. Here are a few benefits you can take advantage of:
Corrosion-Resistant
Silver is one of your best options if you need a material that is resistant to corrosion. By adding this long-lasting coating to your metal substrates, the component will also become corrosion-resistant, giving you the most durable product for your money.
Conductivity
Silver has a high degree of thermal and electrical conductivity, making it the perfect material for uses involving electricity and extreme heat. Due to its conductive qualities, silver is frequently used by engineers working in the aerospace, electronics, and automotive industries.
Lightweight
Despite its toughness, silver is portable and simple to work with. When working with metal components that will eventually join together, high solderability is crucial. Even when applied in incredibly thin layers, such as 0.0003 inches thick, it can impart all of its best qualities.
Antibacterial
The human body is protected from harmful organisms by this noble metal, which also inhibits the growth of bacteria. This quality is essential for a substance that enters or contacts the body through medical equipment like stethoscopes and insulin pumps.
Silver plating is ideal for all products that need a high-quality finish and conductivity because it also offers excellent solderability for small parts like kitchen utensils and little electrical resistance. A silver finish improves the product’s lubricity as well.
Despite the fact that silver-finished products can still tarnish, silver plating is still less expensive than gold plating, which achieves comparable results.
Why Silver?
A brilliant white metallic luster can be seen on pure silver. It is considerably more ductile and malleable and slightly harder than gold. Of all metals, pure silver has the lowest contact resistance and the highest electrical and thermal conductivity.
Silver does not tarnish when exposed to ozone, hydrogen sulfide, or sulfur-containing air, but it does tarnish when exposed to pure air and water. Silver is primarily used in electroplating for industrial purposes, particularly electrical connectors. Additionally, it is used in dinnerware, jewelry, automotive, telecom, and industry.
Potential Drawbacks Of The Silver Plating Process
If you want to keep the appearance of your product, you must apply an anti-tarnish coating to this metal because it can tarnish. Some people might not be concerned about this aspect, but if it is for you, you can choose a tarnish-resistant treatment at that time.
Any metal that has been electroplated frequently experiences a loss of adhesion. The substrate’s surface is primarily responsible for this phenomenon. There could be substances like oils, dust, or particular metal alloys that hinder the effectiveness of the coating.
Any metal you use can cause dull spots to develop on the plating, similar to adhesion loss. These can occur as a result of a number of problems, including an ion solution that is the incorrect temperature or an interrupted flow of electric current. Many of these worries will cease to exist if you choose the right plating specialists. Even though silver is a fantastic metal to work with, mistakes can still happen if the manufacturer doesn’t handle it properly.
Silver Plating Specifications
To achieve the best results when performing silver electroplating, it might be necessary to adhere to predetermined engineering specifications. You always want to get the best value for your time and money when manufacturing metal parts. You can achieve that by studying the specifications and adhering to them. Two different standards exist:
ASTM B700
For engineering-related silver electroplating, these specifications are applicable. MIL-QQ-S-365, the federal silver standard, has been replaced by it. It includes a set of minimum purity requirements that look like this:
- Type I: 99.9 percent silver minimum
- Type II: 99.0 percent silver minimum
- Type III: 98.0 percent silver minimum
A number of specifications related to silver hardness and post-treatment techniques are also included in ASTM B700. In terms of criteria, it is comparable to the QQ-S-365 but is more detailed
- Grade A: Matte — no brighteners in the plating solution.
- Grade B: Bright — brighteners placed in the plating solution.
- Grade C: Bright — Grade A silver that’s received mechanical or chemical polishing.
- Grade D: Semi-bright — brighteners placed in the plating solution.
- Grade N: No chromate treatment.
- Grade S: Supplementary anti-tarnish treatment
MIL-QQ-S-365
Although the ASTM B700 has replaced this federal standard, it is still widely used in engineering organizations, so understanding it is crucial. These specifications describe the different silver finishes and hardness levels:
- Type I: Matte finish
- Type II: Semi-bright finish
- Type III: Bright finish
- Grade A: Supplementary tarnish-resistant treatment
- Grade B: No supplementary tarnish-resistant treatment
When using silver electroplating for functional purposes, this requirement also stipulates that the thickness of the silver plating must be at least 0.0005 inches.
- Grade A: Matte, with no brighteners used in the plating bath
- Grade B: Bright, due to brighteners placed in the plating bath
- Grade C: Bright, due to chemical or mechanical polishing of Grade A silver coatings
- Grade D: Semi-bright, due to brighteners placed in the plating bath
- Class N: Receives no chromate treatment
- Class S: Receives supplementary tarnish-resistant treatment
A specific undercoating standard may also need to be followed by your products. Your product needs to have a nickel-over-copper undercoat if you’re silver-plating steel, zinc, or surfaces made of zinc-based alloys. A nickel undercoat is necessary for silver plating on products made of copper or copper alloys.
Industrial Applications Of Silver Plating
Many industries, including the automotive, medical, electronics, and telecommunications sectors, use silver plating frequently. Due to its versatility, this metal can be used for a variety of purposes, from flatware to wearable medical devices. Silver plating is used on many medical devices to increase their durability and electrical conductivity. Here, the antibacterial properties of silver stand out because it’s crucial to stop the spread of disease in a sterile hospital setting.
Additionally, the renewable energy industry, which is gaining popularity due to its sustainable advantages, uses a lot of silver-plated materials. Numerous businesses create silver-coated solar panels, batteries, and other clean energy products. Silver’s conductive qualities combined with solar energy can reduce electricity costs for both individuals and businesses.
Alternatives To Silver Plating
Not all metals can be used for finishing, including silver. You can use more expensive materials than silver, such as gold, copper, platinum, and palladium. Each type has its own benefits, drawbacks, and guidelines to follow. The conductivity and anti-corrosion qualities of gold plating are excellent, but you should only use this process if the additional costs won’t be a problem for your business.
Palladium works well as an alloying element and has a wide range of industrial uses as a catalyst. Similar to silver, it is lightweight while maintaining a respectable degree of durability, making it appropriate for smaller objects. In the dental sector, this metal is widely used by manufacturers to create items like bridges and crowns.
Common Silver Electroplating Issues
Despite being a successful process, silver electroplating occasionally presents problems, depending on how the manufacturer handles it. For instance, after you’ve finished all pre-treatments, such as machining, soldering, welding, or performing heat treatments, you should only perform silver electroplating on your substrates.
Cracks or hydrogen embrittlement will be problematic during the silver plating process if there are any flaws. If the metal part isn’t properly prepared beforehand, you might run into problems like gaps in the coating coverage and poor adhesion.
Navigating Silver Plating Issues
To navigate through any issues with silver plating consider the following:
Complete Your Treatments
Prior to plating your product, always finish all of your thermal and mechanical treatments. Use lubricants that are easily removed when performing pre-treatment. By taking these preventative measures, you decrease the likelihood that defective products will reach your customers, and you avoid having to create additional substrates, which will save you time.
Avoid Sulfur
Avoid sulfur because it tarnishes silver when it comes into contact with it. The main factor causing this reaction is this substance. Silver-saver paper and other non-sulfuric materials should be used to package your finished products if you don’t want your materials to lose their sheen.
Speak To The Manufacturer
Inform the manufacturer if there are any specific alloys on your substrate that might necessitate the use of a different electroplating method. They’ll know better how to handle your part and employ the proper plating technique to maintain its functionality.
At Valence Surface Technologies, our engineers are always happy to listen to your needs by meeting and exceeding your expectations.
Our Plating Services
Our plating services include the following:
Cadmium Plating
Cadmium plating is a tough and versatile coating. The soft, attractive coating provides a favorable bonding surface for adhesions. It is also the preferred plating for salt-water environments due to its resistance to mold and bacteria.
Chrome Plating
Chromium plating is effective at providing excellent hardness and lubricity, reducing friction, minimizing wear, and preventing galling. In environments with corrosion or abrasion, chrome plating can withstand the negative consequences of wear and tear.
Copper Plating
Copperplate has high electrical conductivity, exceeded only by silver plating. Copper is an excellent and inexpensive coating for many different uses that require conductivity or solderability. As a result of malleability and perfect adhesion, copper can maintain adhesion and serve as a base for added coating and plating.
Electroless Nickel Plating
Electroless nickel plating is a unique process that uses heat and a unique chemical bath to create the nickel without the use of any electrical current. Since electroless nickel finishing does not use electricity, the coating created by the process is very uniform across the entire surface of the part, even parts with complex geometry. Threads and close tolerance features can be plated precisely without edge build-up.
Gold Plating
Gold plating advantages include good corrosion resistance and good solderability, and when alloyed with cobalt, it has very good wear resistance. Gold is commonly used in electrical switch contacts, connector pins and barrels, and other applications where intermittent electrical contact occurs.
It is also used as a radiation shield in infrared reflectors and electronic satellite housings. Valence also offers immersion gold plating.
Manganese Phosphate
Manganese phosphate coating is a conversion coating, the formulation of which contains a manganese salt, phosphoric acid, and an accelerator. This process is done under high temperature and produces a surface that has good corrosion and wears resistance. Manganese phosphate coatings can retain oil and other lubricants.
Nickel Plating
Nickel plating provides exceptional hardness and corrosion/wear resistance. Nickel is one of the four ferromagnetic materials at room temperature and is a fairly active element. However, nickel deposits are slow to react in standard atmospheric environments due to the formation of a protective oxide surface providing excellent corrosion performance on most products.
Nickel Sulfamate
Nickel sulfamate is a plating process that provides a highly ductile plating surface with low internal stress. The versatility of the coating resists high temperatures, maintains high tensile strength, and provides ductility and elongation.
Ti-Cad Plating
Ti-Cad or titanium cadmium plating is a titanium cadmium combination plating that provides corrosion resistance on high-strength steel applications. It significantly reduces the negative consequences of hydrogen embrittlement.
Tin Plating
Tin plating is used extensively to protect both ferrous and nonferrous surfaces. Tin is also widely used in the electronics industry because of its ability to protect the base metal from oxidation and corrosion. Depending on the base material, tin is used as a metal plating to maintain or impart solderability. Valence also offers tin-lead plating.
Final Thoughts
When used carefully and precisely, silver plating can offer you a wide range of advantages. There are many benefits that you can’t always get with other metals, ranging from outstanding conductivity to lower costs.
At Valence Surface Technologies, we provide the degree of precision and consideration necessary to produce an excellent product.
By requesting a free quote from Valence Surface Technologies for your upcoming manufacturing project, you can find out more about the silver plating procedure. For your industrial needs, we can assist you in choosing the plating technique that will produce consistently high-quality and long-lasting results.